China’s Monocrystalline Boom and India implications

Step back to 2003. China’s share of solar cell and modules production was 1.6 percent. In 2018, the country accounts for over 70 percent of global production, and over half its installations in the sector. A figure that could be even higher as 2017 was a standout year for domestic istallations in the home market for Chinese majors.
This incredible performance by Chinese firms has been built on a bedrock of focus, official support, and most importantly, a booming domestic market. And this time, with higher global integration, Chinese manufacturers are doing everything to ensure they retain their leadership in what is essentially a commoditised market. Enter the next level of innovations.
The largest supplier of ingot and wafer in the world along with another Chinese counterpart recently announced plans to exponentially increasing their production capacities for monocrystalline products. Successful execution would mean furthering their dominance of the market, as monocrystalline products are clearly catching on, despite the higher prices.
As part of its wave of expansion, LONGi Solar is in the process of building two massive ingot facilities in Lijiang and Baoshan in the Yunnan Province of China. They’ll supply to their sister facility in the Chuxiong Prefecture of the same province, a wafer slicing facility which processes mono-crystalline silicon, and slices it into wafers as the raw material for solar cells. Another ingot pulling and wafer slicing is under construction in the Ningxia region of North-western China.
IHS Markit have released early estimates that LONGi will nearly double its ingot and wafer capacity to 22.5 GW by the end of this year, from 13.5 GW last year.
Another key manufacturer in the field, Zhonghuan Semiconductor will double their facilities annual production capacity from 5 GW to 10 GW once the fourth face of the facility nesting in inner Mongolia is completed, and the new machines and ingot furnaces are ready to be pushed. This combined with a brand new 10 GW annual capacity plant in the Yunnan Province.
Why mono over multicrystalline?
Monocrystalline Silicon is developed from a single crystal using the Czochralski Method in Ingot furnaces. The cells that are made from these wafers offer more room to move for the electrons which generate the flow of electricity. As a result, monocrystalline panels offer more efficiency than their poly/multicrystalline counterparts.
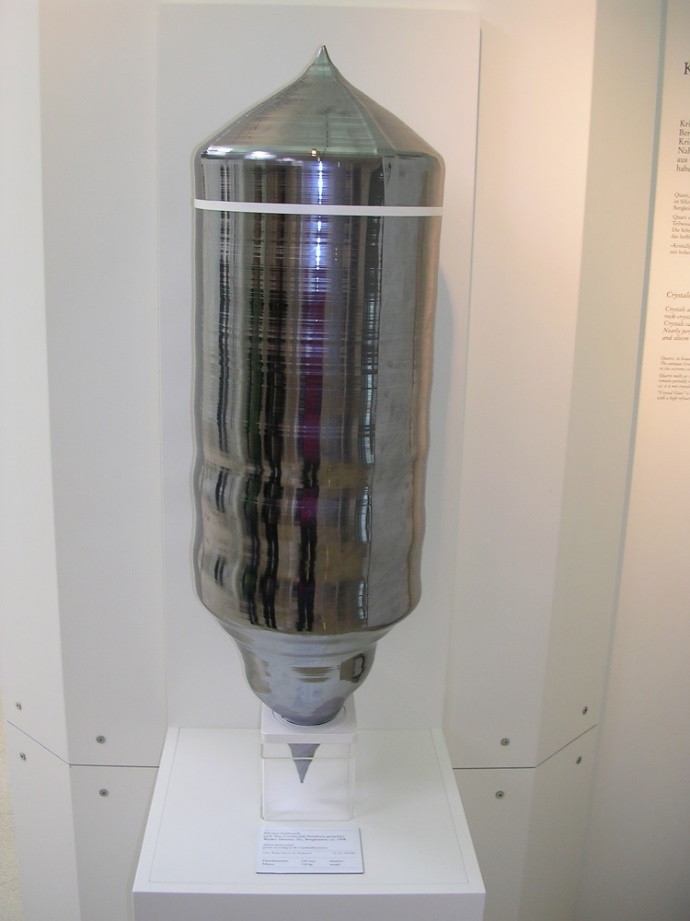
Upstream and Downstream effects? The process uses multicrystalline silicon as raw material, then using a seed crystal a long tube of single crystal silicon (as seen in the picture) is pulled out from the molten mass of silicon. Which are then sewn into semi-square blocks and sliced into wafers. Unlike multicrystalline which is made from melting together many fragments of silicon to form the wafer. Due to this extra process it is inherently more expensive to make but offers higher resistance to cracking during the cell and module production process.
2016 witnessed an increased demand in mono, driving the sales and prices up. However this led to a shortage of mono products due to a demand that couldn’t even be tamed by multiple factories coming online. The demands soared when during the “Top Runners” program, a reverse auction program for high efficiency products, mono made up 40% of China’s demand.
Interestingly for the industry in India, and in a point already made by the Ministry of New and Renewable Energy, the country’s solar cell and module industry has already been declared ‘obsolete’ by the MNRE, owing to their dependence on a multicrystalline product line up. In fact, this is one of the reasons developers are unable to find the level of sympathy one would expect for Indian manufacturers. As they clearly want to move to the more efficient monocrystalline films.
To meet its massive demands to produce enormous ingots and wafers, LONGi and Zhonghuan need a supply of polysilicon to cast ingots which is bound to change the upstream landscape.
To meet its needs LONGi recently signed a 3 year or 64,600 metric tonnes of polysilicon deal with South Korea’s OCI worth $1 billion. Dr. Tian Xie, director of quality management at LONGi said,” Concerning the quality of OCI’s polysilicon, it is good and better than done other players in China.” He also added, “For the future we can see a lot of improvements in Chinese makers, they are doing a lot of activities to improve the quality of their products, and the quality gap between OCI and these poly makers will become smaller and smaller.” Xie told PV magazine.
Zhonghuan source their polysilicon from GCL, Wacker and OCI. Having also entered a joint venture with GCL for the supply of polysilicon from it’s under construction plant and also bring on board is technological and financial prowess.
This mono expansion by LONGi who plan to reach 45 GW annual capacity by 2020 using their highly efficient and economical machines and method of manufacturing and Zhonghuan who have developed presence all over China will provide a substantial boom to the upstream solar energy businesses.
Downstream, the market for the unprecedented quantity of mono wafers that these two will be producing still remains a little uncertain and hinged on the predicted demand growth of Monocrystalline products. LONGi believe they are enabling the industry shift from multi to mono, by producing high efficiency and more durable mono products in the multi silicon based market. This is due to their technology that yielded low productions costs.
Other market drivers will be the success of P-PERC (Passivated Emitter Rear Contact) cells based on P type mono wafers in which recently LONGi achieved the new world record for maximum efficiency at 23.6%. “We believe that P-PERC will be mainstream in the next few years,” predicts Xie.